
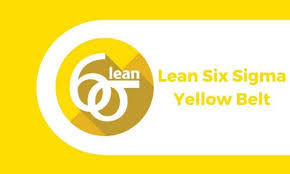
Six Sigma Yellow Belt Certification
Our Six Sigma Yellow Belt certification training provides an introductory overview of Six Sigma principles and methodologies, equipping you with the essential knowledge to contribute to process improvement efforts. This program focuses on the core concepts of the DMAIC methodology, allowing you to understand the fundamental steps involved in process optimization. You'll learn to identify areas for improvement and understand the basic tools and techniques used in Six Sigma projects. Our instructors provide practical, hands-on training, utilizing real-world examples to enhance your learning. You'll gain the ability to understand how data analysis and process improvement contribute to organizational success. This training program allows you to become a valuable contributor to improvement teams and prepare for the Yellow Belt certification. Gain the foundational knowledge needed to understand and support Six Sigma initiatives. Key phrases: Six Sigma Yellow Belt, Yellow Belt training, Six Sigma certification course, DMAIC introduction, process improvement basics, quality awareness training.
Course Overview:
This course by 4D – The Fourth Dimension Training and Consultancy provides participants with a solid foundation in the Six Sigma methodology, focusing on the Yellow Belt level. It introduces the key concepts of process improvement, quality control, and problem-solving using the DMAIC (Define, Measure, Analyze, Improve, Control) framework. Participants will understand how to contribute to Six Sigma projects as effective team members, apply quality tools, and support process improvement initiatives within their organizations.
Course Objectives:
By the end of this course, participants will be able to:
○ Understand the philosophy and goals of Six Sigma
○ Describe the DMAIC methodology and apply its steps
○ Identify waste and variation in processes
○ Use basic quality tools for data analysis and problem solving
○ Support Green Belt or Black Belt-led projects
○ Contribute to continuous improvement and quality initiatives
Target Audience:
○ Entry-level quality and process improvement professionals
○ Team members involved in Six Sigma or Lean initiatives
○ Production, operations, and service staff
○ Supervisors and junior managers
○ Anyone interested in foundational process improvement knowledge
Course Delivery Method:
○ Instructor-led (classroom or virtual)
○ Interactive workshops and team activities
○ Real-life examples and Six Sigma project case studies
○ Hands-on exercises with templates and tools
Course Outlines
Module 1: Introduction to Six Sigma
○ What is Six Sigma?
○ History and evolution of Six Sigma
○ Benefits of Six Sigma in organizations
○ Roles and responsibilities (Yellow, Green, Black Belts)
Module 2: DMAIC Methodology Overview
○ Define – Identifying problems and project goals
○ Measure – Collecting data and identifying current performance
○ Analyze – Root cause identification
○ Improve – Generating and implementing solutions
○ Control – Sustaining improvements
Module 3: Process Mapping and Waste Identification
○ SIPOC diagram creation
○ Process flowcharting
○ Identifying non-value-added activities (waste)
○ Basics of Lean principles
Module 4: Data Collection and Basic Quality Tools
○ Introduction to data types and data collection plans
○ Pareto charts and cause-and-effect diagrams
○ Histogram, control charts, and scatter diagrams
○ Basic statistical concepts (mean, median, standard deviation)
Module 5: Problem Solving and Root Cause Analysis
○ The 5 Whys technique
○ Fishbone (Ishikawa) diagrams
○ Brainstorming and prioritization tools
○ Simple root cause validation techniques
Module 6: Sustaining and Supporting Six Sigma Projects
○ Monitoring improvement initiatives
○ Supporting Green Belt/Black Belt teams
○ Communicating project progress and impact
○ Building a culture of quality and continuous improvement